
SolidThinking is a wholly owned subsidiary of Altair. “We are excited to be deploying this technology through our global channel partners with their deep domain knowledge and expertise.” Scapa, Altair founder, chairman and CEO, in a press statement. “Inspire embodies our vision to make simulation available across multiple user communities to facilitate innovation,” says James R. Inspire 2016 has been enhanced with buckling analysis capabilities. Other tools in the PolyNURBS toolset include +/- (add/remove) for adding a new cage to the face of an existing cage, Loop for drawing an edge loop around a cage and Bridge for connecting two cages together. The new PolyNURBS toolset contains a number of tools new to Inspire, including Create for making free-form solid geometry and a Wrap tool that allows users to generate PolyNURBS geometry by clicking along the contour of an existing shape. “The result is an incredibly robust tool that has not only expanded the use cases for Inspire, but also accelerates the path to cost-effective manufacturing.” “Our new PolyNURBS toolset is a game changer, allowing users to create geometry from optimized results much faster than traditional CAD modeling,” said Andy Bartels, program manager, in a press statement. Inspire supports such export formats as ACIS, IGES, Parasolid, STEP and STL.
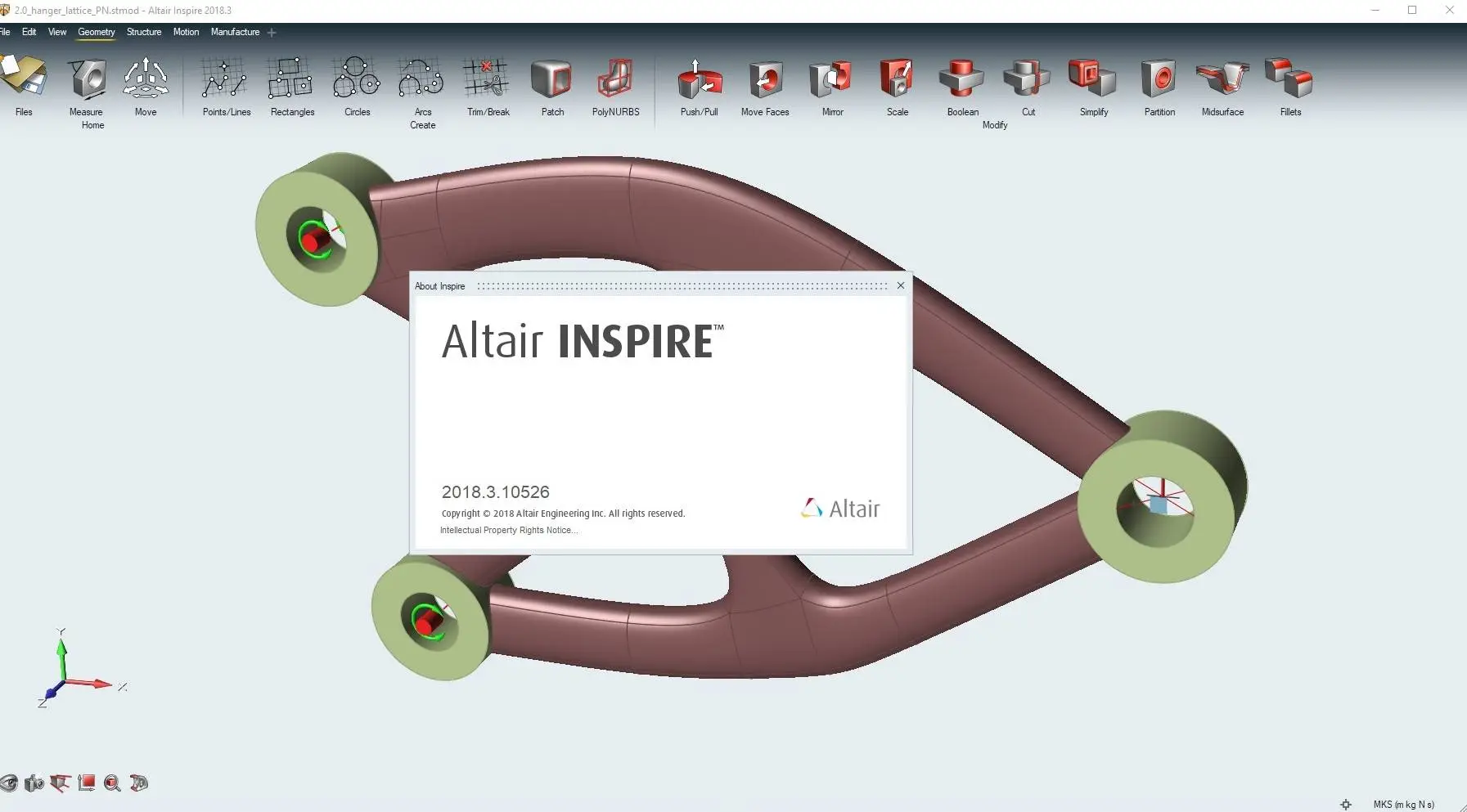
Users can then flow optimized designs into products that can be fabricated in a 3D printing process.

Inspire 2016’s new PolyNURBS functionality allows designers and engineers to create free-form solid geometry that is smooth and continuous by wrapping topology results with NURBS geometry. Here, Inspire 2016 has been used to optimize and prepare an engine block mount design for an additive manufacturing process. Inspire 2016’s new PolyNURBS toolset enables designers and engineers to create free-form solid geometry that’s wrapped with NURBS geometry.
